Turbinas de gas que ahorran energía gracias a la impresora 3D
Los neutrones "ven" la tensión interna en los componentes de la fabricación aditiva
La impresión 3D ha abierto un abanico de posibilidades completamente nuevo. Un ejemplo es la producción de novedosas cucharas para turbinas. Sin embargo, el proceso de impresión en 3D suele inducir tensiones internas en los componentes que, en el peor de los casos, pueden provocar grietas. Ahora, un equipo de investigación ha conseguido utilizar los neutrones del reactor de la fuente de neutrones de investigación de la Universidad Técnica de Múnich (TUM) para detectar de forma no destructiva esta tensión interna, un logro clave para la mejora de los procesos de producción.
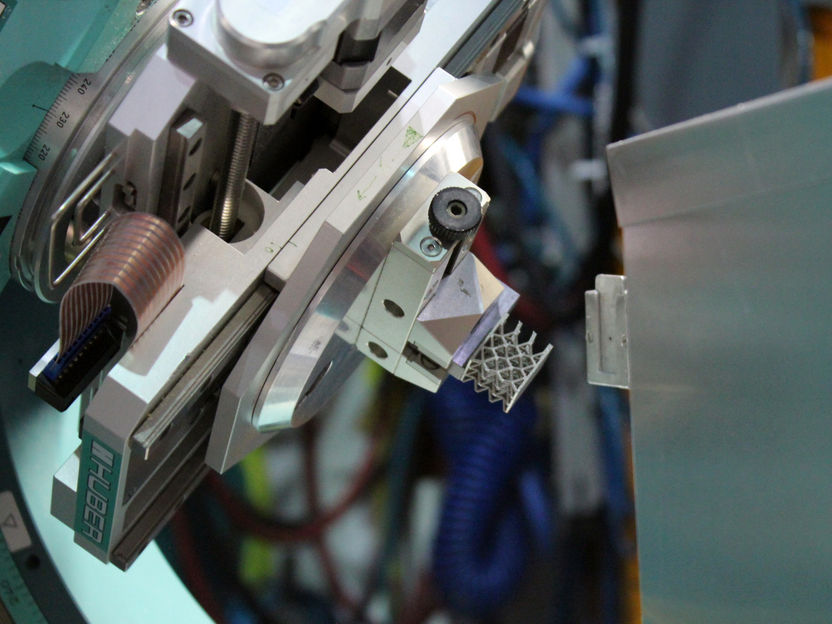
La estructura de la red en la posición de medición en el difractómetro de tensiones residuales STRESS-SPEC.
Tobias Fritsch / BAM
Los cangilones de las turbinas de gas tienen que soportar condiciones extremas: Están expuestos a tremendas fuerzas centrífugas bajo alta presión y a altas temperaturas. Para maximizar aún más el rendimiento energético, los cangilones tienen que aguantar temperaturas incluso superiores al punto de fusión del material. Esto es posible gracias a los cangilones de turbina huecos que se refrigeran con aire desde el interior.
Estos cubos de turbina se pueden fabricar mediante la fusión de lechos de polvo por láser, una tecnología de fabricación aditiva: en ella, el material de partida en forma de polvo se construye capa a capa mediante la fusión selectiva con un láser. Siguiendo el ejemplo de los huesos de las aves, las intrincadas estructuras reticulares del interior de los cubos huecos de las turbinas proporcionan a la pieza la estabilidad necesaria.
El proceso de fabricación crea tensiones internas en el material
"Los componentes complejos con estructuras tan complejas serían imposibles de fabricar con métodos convencionales como la fundición o el fresado", explica el Dr. Tobias Fritsch, del Instituto Federal Alemán de Investigación y Ensayo de Materiales (BAM).
Pero el aporte de calor muy localizado del láser y el rápido enfriamiento del baño de fusión provocan tensiones residuales en el material. Los fabricantes suelen eliminar estas tensiones en una fase posterior de tratamiento térmico, que sin embargo lleva tiempo y cuesta dinero.
Desgraciadamente, estas tensiones también pueden dañar los componentes ya durante el proceso de producción y hasta el postratamiento. "Las tensiones pueden provocar deformaciones y, en el peor de los casos, grietas", afirma Tobias Fritsch.
Por ello, investigó la tensión interna de un componente de turbina de gas utilizando neutrones de la Fuente de Neutrones de Investigación Heinz Maier-Leibnitz (FRM II). El componente fue fabricado mediante procesos de producción aditiva por el fabricante de turbinas de gas Siemens Energy.
Se omite intencionadamente el posprocesamiento
Para el experimento de neutrones en la FRM II, Siemens Energy imprimió una estructura reticular de unos pocos milímetros de tamaño utilizando una aleación de níquel y cromo típica de las utilizadas para los componentes de las turbinas de gas. Se omitió intencionadamente el tratamiento térmico habitual tras la producción.
"Queríamos ver si podíamos utilizar los neutrones para detectar tensiones internas en este complejo componente", explica Tobias Fritsch. Ya había adquirido experiencia con las mediciones de neutrones en el reactor de investigación BER II de Berlín, que sin embargo se cerró a finales de 2019.
"Estamos muy contentos de poder realizar mediciones en el Heinz Maier-Leibnitz Zentrum de Garching; con el equipo proporcionado por STRESS-SPEC pudimos incluso resolver las tensiones internas en estructuras reticulares tan intrincadas y complejas como estas", afirma el físico.
Distribución uniforme del calor durante la impresión
Ahora que el equipo ha conseguido detectar la tensión interna en el componente, el siguiente paso es reducir esta tensión destructiva. "Sabemos que tenemos que modificar los parámetros del proceso de producción y, por tanto, la forma en que se construye el componente durante la impresión", dice Fritsch. En este caso, el factor crucial es el aporte de calor a lo largo del tiempo cuando se construyen las capas individuales. "Cuanto más localizada esté la aplicación de calor durante el proceso de fusión, más tensiones internas se producen".
Mientras el láser de la impresora se dirige a un punto determinado, el calor del punto aumenta en relación con las zonas adyacentes. Esto da lugar a gradientes de temperatura que provocan irregularidades en la red atómica.
"Así que tenemos que distribuir el calor de la forma más uniforme posible durante el proceso de impresión", dice Fritsch. En el futuro, el grupo investigará la situación con nuevos componentes y parámetros de impresión modificados. El equipo ya está trabajando con Siemens para planificar nuevas mediciones con la fuente de neutrones de la TUM en Garching.
Nota: Este artículo ha sido traducido utilizando un sistema informático sin intervención humana. LUMITOS ofrece estas traducciones automáticas para presentar una gama más amplia de noticias de actualidad. Como este artículo ha sido traducido con traducción automática, es posible que contenga errores de vocabulario, sintaxis o gramática. El artículo original en Inglés se puede encontrar aquí.