Visión de rayos X de la producción de hidrógeno
El análisis señala el camino hacia electrodos de iridio más duraderos
Se espera que el hidrógeno verde desempeñe un papel fundamental en la industria energética del futuro: Entre otras cosas, puede sustituir al petróleo y al gas como vectores energéticos y también permitir la producción de acero y cemento sin emisiones. Sin embargo, para que la economía del hidrógeno sea eficiente, es necesario mejorar la producción del gas que contiene la energía. Investigadores del DESY, la Universidad Justus Liebig de Giessen, las Universidades de Lund y Copenhague y el Instituto Helmholtz de Erlangen-Nuremberg para Energías Renovables han investigado ahora el costoso desgaste de los electrodos para la producción de hidrógeno en la fuente de luz de rayos X PETRA III del DESY. El análisis señala el camino hacia electrodos más duraderos, como informa el equipo en la revista ACS Catalysis de la Sociedad Química Americana (ACS).
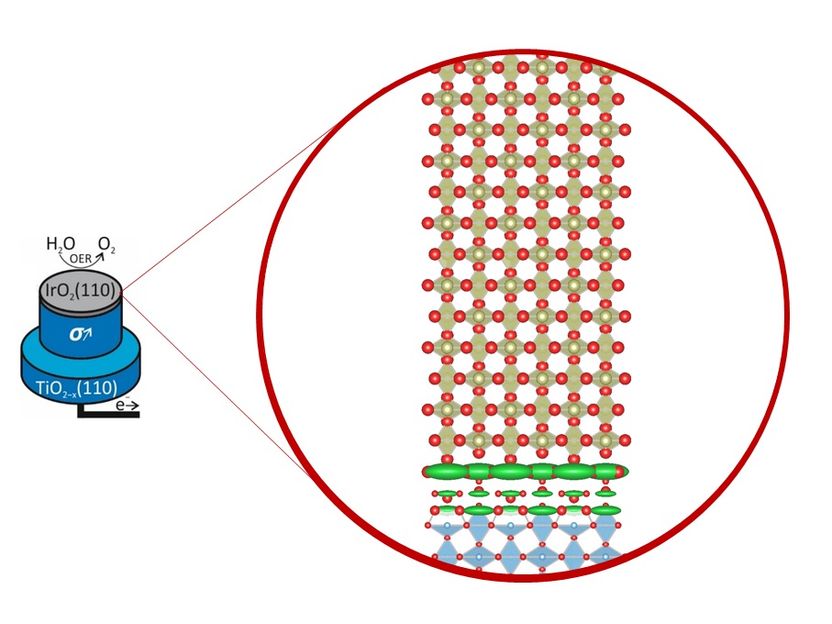
Si los electrodos para la producción de hidrógeno se recubren de forma especialmente uniforme con iridio estabilizador, no se desgastan tan rápidamente. Esta idea puede hacer que la división eléctrica del agua (electrólisis) sea más eficiente.
DESY, Vedran Vonk
El hidrógeno verde, o climáticamente neutro, se produce hoy en día con los llamados electrolizadores. Con la ayuda de la electricidad procedente de energías renovables, dividen el agua en sus componentes oxígeno e hidrógeno. Para que esta división de moléculas funcione, es necesario hacer pasar la corriente a través de una solución ácida reactiva. Para ello se utilizan electrodos muy resistentes a la corrosión, que también sirven de catalizadores y aceleran decisivamente la reacción. Uno de los materiales utilizados para ello es el raro metal precioso iridio: en muchos electrolizadores, los ánodos están recubiertos con una fina capa de óxido de iridio. El problema es que estos recubrimientos se desgastan con el tiempo y se corroen. Esto reduce la durabilidad del equipo y encarece los costes de producción.
Con la ayuda de los rayos X de PETRA III, los investigadores examinaron de cerca los posibles procesos de desgaste. Para crear condiciones realistas, los expertos sumergieron una fina capa de óxido de iridio en un electrolito y aplicaron una corriente eléctrica. "A continuación, utilizamos el haz de rayos X focalizado de la línea de luz P21.2 para observar lo que ocurría durante varias horas", explica el coautor Tim Weber, de la Universidad de Gießen. "A partir de los datos de las mediciones, pudimos registrar con precisión si el grosor y la rugosidad de la capa cambiaban y cómo lo hacían". El electrolito puede ser penetrado fácilmente por el haz de rayos X, y el método de medición es tan rápido que incluso los cambios estructurales rápidos podrían ser monitoreados.
Las capas de óxido de iridio examinadas en el estudio tenían una calidad especialmente buena y uniforme, porque fueron producidas con un proceso de alta precisión por el equipo de Herbert Over en la Universidad de Giessen. "La capa de cinco nanómetros de espesor se mantuvo prácticamente constante durante nuestras mediciones", afirma el coautor Vedran Vonk, del NanoLab del DESY. "Ni el grosor ni la estructura cristalina cambiaron de forma apreciable". Estos resultados proporcionan a la industria una pista importante: cuanto mejor y más uniforme sea el recubrimiento con óxido de iridio, más estables y duraderos serán los ánodos y más económicos podrán funcionar los electrolizadores a largo plazo. "Sólo si conseguimos entender los procesos de corrosión a escala atómica tendremos también la oportunidad de buscar materiales que puedan sustituir al iridio", afirma Over, que dirigió el estudio. Los resultados actuales son un paso importante en esta dirección.
Nota: Este artículo ha sido traducido utilizando un sistema informático sin intervención humana. LUMITOS ofrece estas traducciones automáticas para presentar una gama más amplia de noticias de actualidad. Como este artículo ha sido traducido con traducción automática, es posible que contenga errores de vocabulario, sintaxis o gramática. El artículo original en Inglés se puede encontrar aquí.
Publicación original
T. Weber, V. Vonk, D. Escalera-López, G. Abbondanza, A. Larsson, V. Koller, M.J.S. Abb, Z. Hegedüs, T. Bäcker, U. Lienert, G.S. Harlow, A. Stierle, S. Cherevko, E. Lundgren, H. Over; "Operando Stability Studies of Ultrathin Single-Crystalline IrO2(110) Films under Acidic Oxygen Evolution Reaction Conditions"; ACS Catalysis; 2021