Lucha contra los microplásticos con láser
Primer filtro perforado por láser para la filtración de microplásticos de las aguas residuales
Hasta ahora, las plantas de tratamiento de aguas residuales no han sido capaces de filtrar suficientemente los diminutos microplásticos presentes en las aguas residuales, pero esto podría cambiar pronto: El primer filtro de microplásticos perforado con láser se está probando en una planta de tratamiento de aguas residuales. Contiene láminas con agujeros extremadamente pequeños de apenas 10 micrómetros de diámetro. La tecnología para perforar eficazmente millones de agujeros de este tipo se desarrolló en el Instituto Fraunhofer de Tecnología Láser ILT, y ahora los ingenieros del instituto están ampliando la tecnología láser de ultracorriente (USP) en el rango de los kW. Los visitantes pueden obtener más información sobre el filtro de microplásticos y los láseres de ultracorriente en el stand A6.441 de Fraunhofer en LASER World of PHOTONICS.
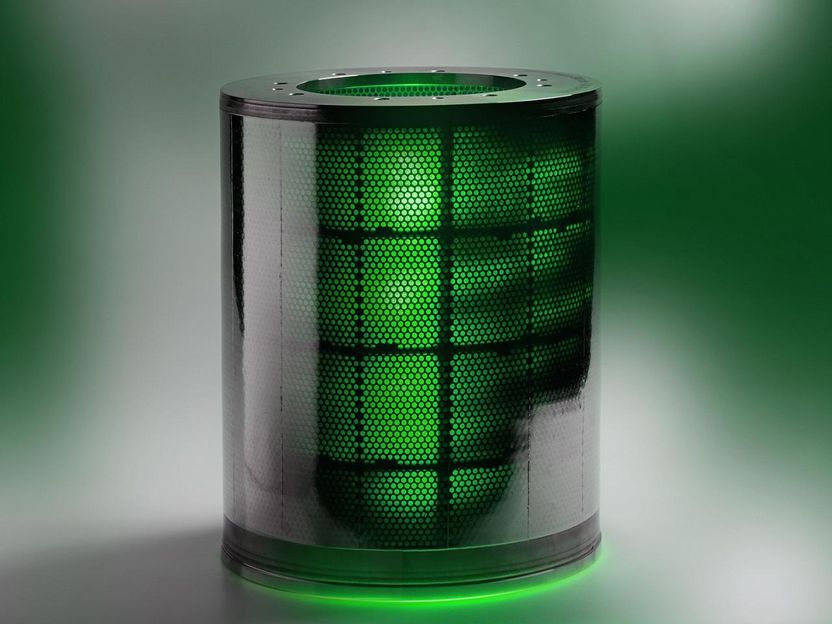
59 millones de agujeros en la placa filtrante del primer filtro perforado por láser para la filtración de microplásticos de las aguas residuales municipales.
© Fraunhofer ILT, Aachen
Hoy en día, la sostenibilidad no es una opción, sino mucho más una obligación, independientemente de la tecnología que se esté desarrollando. En consecuencia, la industria del láser utiliza cada vez más la tecnología USP para mejorar la sostenibilidad en muchos proyectos. Los láseres ya se utilizan para aumentar la eficiencia de la tecnología del hidrógeno y para generar carcasas de baterías absolutamente herméticas en aplicaciones de electromovilidad.
En el proyecto SimConDrill, financiado por el BMBF, Fraunhofer ILT ha unido fuerzas con socios industriales para construir un filtro que, por primera vez, puede eliminar microplásticos de las aguas residuales. "En esencia, nuestro reto consistía en perforar el mayor número posible de agujeros, lo más pequeños posible, en una lámina de acero en el menor tiempo posible", explica Andrea Lanfermann, directora del proyecto en Fraunhofer ILT.
Planta de filtrado móvil en una planta de tratamiento de aguas residuales
Esto se ha conseguido. Después de desarrollar el proceso en el Fraunhofer ILT, los expertos de LaserJob GmbH perforaron 59 millones de agujeros con un diámetro de 10 micrómetros en una lámina filtrante, creando así un prototipo de filtro. Los investigadores del Fraunhofer también colaboran con otras tres empresas en este ambicioso proyecto. Además del coordinador del proyecto, KLASS Filter GmbH, también participan LUNOVU GmbH y OptiY GmbH.
Entretanto, las láminas metálicas perforadas por láser se han instalado en el filtro ciclónico patentado de KLASS Filter GmbH y se han sometido a extensas pruebas. En la primera prueba, se filtró el polvo fino de las impresoras 3D del agua contaminada. El montaje se está probando ahora en condiciones reales en una planta de tratamiento de aguas residuales.
El conocimiento del proceso es la clave
Perforar millones de agujeros uno tras otro lleva tiempo, pero puede hacerse más rápido con el proceso multihaz, en el que se genera una matriz de haces idénticos a partir de un rayo láser mediante un sistema óptico especial. Fraunhofer ILT utilizó este proceso con un láser de pulso ultracorto (TruMicro 5280 Femto Edition) para perforar agujeros simultáneamente con 144 haces. La base de este tipo de aplicaciones es el conocimiento detallado del proceso, que se ha recopilado en Fraunhofer ILT durante décadas y se ha implementado en los modelos y el software correspondientes. Gracias a estos conocimientos, se pueden variar los parámetros en el ordenador y encontrar rápidamente los parámetros óptimos del proceso. También se puede analizar la robustez del proceso antes de probar la aplicación.
Paralelamente a esta aplicación de perforación, un consorcio de seis socios trabaja en la mejor manera de integrar un sistema de procesamiento multihaz en una máquina industrial. En el proyecto de la UE Multiflex, los investigadores, junto con la industria, están aumentando la productividad del procesamiento de materiales por láser con escáner mediante procesos multihaz. La particularidad de este proyecto es que todos los haces parciales pueden controlarse individualmente y, por tanto, utilizarse para producir cualquier tipo de estructura superficial. Los socios del proyecto pretenden aumentar la velocidad del proceso entre veinte y cincuenta veces, con lo que todo el proceso será mucho más rentable.
CAPS: Escala en el rango de los kW
El conocimiento del proceso también es un factor crítico para seguir ampliando el procesamiento de materiales con pulsos láser ultracortos con o sin óptica multihaz. Cuando se aumenta la potencia hasta el rango de los kilovatios, pueden producirse daños térmicos en la pieza. Estos efectos se exploran mediante complejas simulaciones, y los procesos pueden adaptarse en consecuencia.
Los sistemas láser para estos experimentos están disponibles en el laboratorio de aplicaciones del Fraunhofer ILT de Aquisgrán. Forman parte del Fraunhofer Cluster of Excellence Advanced Photon Sources CAPS, donde 13 institutos Fraunhofer desarrollan conjuntamente fuentes de rayos láser, tecnología de procesos y aplicaciones para potencias de láser USP de hasta 20 kW. Un segundo laboratorio CAPS funciona en el Fraunhofer IOF de Jena.
Nota: Este artículo ha sido traducido utilizando un sistema informático sin intervención humana. LUMITOS ofrece estas traducciones automáticas para presentar una gama más amplia de noticias de actualidad. Como este artículo ha sido traducido con traducción automática, es posible que contenga errores de vocabulario, sintaxis o gramática. El artículo original en Inglés se puede encontrar aquí.