Nuevos enfoques en la producción de pilas
De la transformación de materias primas al reciclado
La producción de baterías ocupa un lugar central en la política industrial y climática de todo el mundo. De hecho, la demanda de sistemas de almacenamiento de energía para aplicaciones de electromovilidad y estacionarias está creciendo en todo el mundo, al igual que la importancia de una producción de baterías eficiente, sostenible y regionalmente independiente.
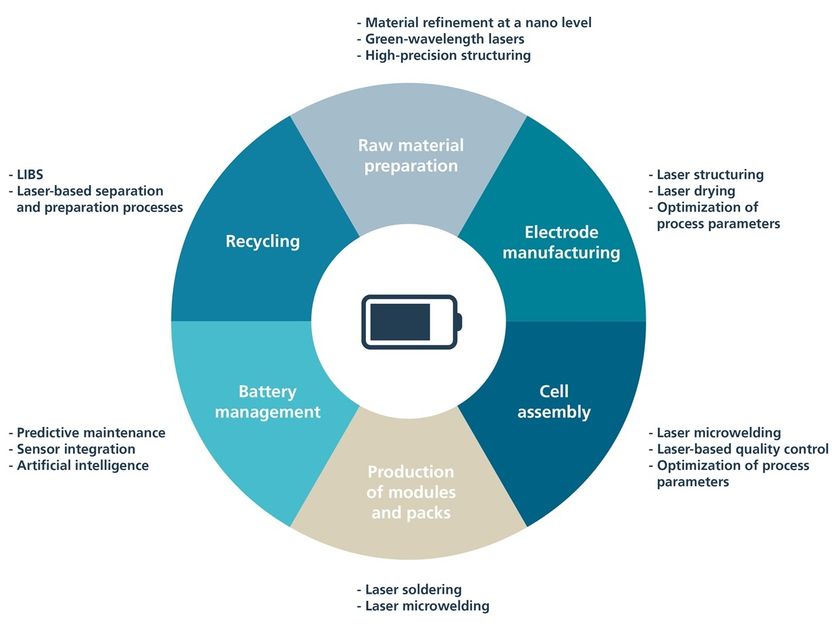
Uso del láser y la IA para la producción sostenible de baterías: producción rentable y fiable.
© Fraunhofer ILT, Aachen
En particular, el entorno empresarial y normativo de la producción de baterías plantea a las empresas inmensos retos: Por ejemplo, la dependencia de materias primas como el litio, el cobalto y el níquel está provocando tensiones geopolíticas. Al mismo tiempo, las cadenas de suministro son cada vez más frágiles a medida que se acumulan las crisis mundiales y aumentan los costes de transporte. Europa se enfrenta, por tanto, a la tarea de construir una cadena de valor resistente que incluya tanto la extracción de materias primas como su posterior procesamiento y reciclado; al fin y al cabo, las baterías usadas son el recurso de litio alemán más abundante. Además, los procesos de producción deben adaptarse con flexibilidad a los nuevos diseños de baterías, como las de estado sólido o las de iones de sodio, para garantizar las inversiones en ellas.
A la vista de estos retos, está claro que el futuro de la producción de baterías en Europa sólo puede asegurarse utilizando tecnologías de vanguardia. La tecnología láser, en particular, ofrece soluciones para satisfacer los requisitos clave: eficiencia, precisión y sostenibilidad. La producción competitiva y sostenible de baterías en Europa es difícilmente concebible sin procesos láser innovadores, ya sea en el procesamiento de materiales, la producción de electrodos o el reciclaje.
Procesamiento de materias primas y refinamiento de materiales: la base para una producción de baterías sostenible
Materiales como el litio y el níquel siguen siendo componentes de las pilas actuales. Sus propiedades químicas y físicas hacen posibles altas densidades de energía y largas vidas útiles, pero su extracción y procesamiento plantean problemas complejos.
Sin embargo, las tecnologías de baterías evolucionan con rapidez y la industria aspira a minimizar el uso de materias primas raras y caras. El fabricante chino de baterías CATL presentó en 2021 una batería de iones de sodio que prescinde por completo del litio y el cobalto. En abril de 2024, CATL lanzó una batería de fosfato de hierro y litio (LFP) sin cobalto que puede propulsar un automóvil durante más de 1.000 kilómetros con una sola carga. En sólo diez minutos puede cargar energía suficiente para 600 kilómetros, lo que corresponde a una velocidad de carga de un kilómetro por segundo.
Toyota tiene previsto utilizar baterías de estado sólido en vehículos híbridos a partir de 2025. Nissan ha puesto en marcha en Japón una planta prototipo de producción de baterías de estado sólido laminadas. Panasonic ha presentado una batería de estado sólido para drones. VW y Mercedes, Ford y BMW están a punto de introducir baterías de estado sólido o han establecido asociaciones estratégicas.
Un punto de partida clave para las nuevas tecnologías de baterías es el perfeccionamiento de materiales a nivel nanométrico; aquí, las materias primas se procesan y funcionalizan específicamente para maximizar su rendimiento en baterías. Esto es lo que está estudiando el Departamento de Tecnología de Superficies y Ablación del Instituto Fraunhofer de Tecnología Láser. Con las modernas tecnologías láser puede intervenir con precisión en la estructura del material y minimizar al mismo tiempo el consumo de recursos.
Otro ejemplo del uso con éxito de las tecnologías láser lo encontramos en la colaboración entre el Fraunhofer ILT, la Cátedra de Tecnología Láser LLT de la Universidad RWTH de Aquisgrán, TRUMPF y el Sincrotrón Alemán de Electrones DESY. Utilizando los rayos X de un acelerador de partículas, los ingenieros han podido profundizar en los procesos de soldadura láser. Demostraron que el uso de láseres con una longitud de onda verde mejora el aprovechamiento del material y reduce los residuos. Sus hallazgos no sólo ofrecen ventajas tecnológicas, sino que también contribuyen a una producción más sostenible.
"Estos proyectos demuestran que la tecnología láser innovadora no sólo puede superar los retos del procesamiento de materias primas, sino también permitir una producción de baterías sostenible y competitiva en Europa", explica el Dr. Alexander Olowinsky, responsable de Unión y Corte de Fraunhofer ILT.
Producción de electrodos: innovaciones para una producción sostenible
Las láminas conductoras de corriente (cobre o aluminio) tienen que recubrirse con los materiales de electrodo para el ánodo y el cátodo, y posteriormente secarse, pasos cruciales que influyen tanto en la densidad energética como en la vida útil de las baterías. Sin embargo, los procesos de secado convencionales basados en hornos de convección consumen una cantidad considerable de energía y requieren mucho espacio, lo que limita la sostenibilidad y la eficiencia de la producción de baterías.
El proyecto IDEEL (Implementation of Laser Drying Processes for Economical & Ecological Lithium- Ion Battery Production), financiado por el Ministerio Federal de Educación e Investigación alemán, muestra cómo el secado por láser resuelve estos problemas: En el proyecto se secaron por primera vez ánodos y cátodos en un proceso rollo a rollo utilizando un láser de diodo de alta potencia. Este método reduce considerablemente el consumo de energía, duplica la velocidad de secado y reduce a la mitad el espacio necesario.
"El secado por láser no sólo permite un control más eficiente del proceso, sino que también ayuda a mejorar significativamente la huella de carbono de la producción de baterías", explica el Dr. Samuel Moritz Fink, director del grupo de Procesado de Películas Delgadas de Fraunhofer ILT. Junto con los socios del proyecto, Fink y su equipo han desarrollado un módulo de secado por láser con óptica adaptada y supervisión del proceso para garantizar un secado uniforme. Este enfoque también ofrece flexibilidad: Los hornos de convección existentes pueden reequiparse con la tecnología láser, lo que facilita la implantación del innovador proceso en las líneas de producción existentes.
En otro proyecto de investigación, Fraunhofer ILT está utilizando una óptica multihaz especialmente desarrollada. Este conjunto óptico divide el haz láser en varios haces parciales que procesan simultáneamente una cinta de 250 milímetros de ancho de un ánodo de batería de iones de litio. Esta estructuración de alta precisión aumenta la densidad energética y mejora la capacidad de carga rápida.
La producción de electrodos también se beneficia de la integración de la inteligencia artificial en el proceso de fabricación. Los investigadores del Fraunhofer ILT están estudiando cómo utilizar sistemas asistidos por IA para optimizar los parámetros del proceso. Estos sistemas no sólo pueden aumentar aún más la calidad y la productividad, sino también sentar las bases para la producción autónoma.
Montaje de células: precisión y eficiencia gracias a tecnologías innovadoras
Además del secado de los electrodos, la unión precisa de los materiales de los electrodos también desempeña un papel fundamental en el rendimiento y la fiabilidad de las pilas. La microsoldadura láser se ha consolidado como una tecnología clave en este ámbito, ya que puede unir materiales como el cobre y el aluminio, esenciales para los electrodos de las baterías, sin entrar en contacto con ellos y con gran precisión. Gracias a la baja carga térmica, la sensible química de la célula permanece intacta, mientras que la conductividad eléctrica se optimiza mediante la reducción de la resistencia de contacto. La microsoldadura láser ofrece una combinación de flexibilidad y eficacia que los procesos de soldadura tradicionales no pueden igualar.
Los requisitos de la microsoldadura láser varían en función del formato de la célula, ya que cada tipo de célula presenta retos específicos a la hora del contacto. Las células cilíndricas requieren una profundidad de soldadura precisa para garantizar la conductividad eléctrica, por un lado, y evitar daños por sobrecalentamiento, por otro. El contacto con el polo negativo plantea especiales dificultades, ya que un calor excesivo puede dañar la sensible junta de polímero, lo que podría provocar fugas de electrolito. En el caso de las pilas de bolsa, que se caracterizan por su diseño flexible y su alta densidad energética, debe evitarse la soldadura a través del recubrimiento de película sensible.
Un avance prometedor en el montaje de células es el proyecto XProLas, que TRUMPF está llevando a cabo en colaboración con Fraunhofer ILT y otros socios. Su objetivo es desarrollar fuentes de rayos X compactas y accionadas por láser que permitan realizar pruebas de calidad in situ directamente en las instalaciones del fabricante, en lugar de utilizar grandes aceleradores de partículas como se hacía hasta ahora. Esta nueva tecnología hace posible analizar las celdas de las baterías en tiempo real, lo que permite controlar con precisión tanto los procesos de carga y descarga como la calidad del material. Este método abre nuevas posibilidades, sobre todo cuando hay que examinar el material del cátodo, que determina el rendimiento y la durabilidad de la batería. "Utilizando fuentes de rayos X brillantes, podemos detectar impurezas y defectos del material en una fase temprana y, de este modo, acortar significativamente los tiempos de desarrollo", explica el ingeniero Hans-Dieter Hoffmann, jefe del Departamento de Láseres y Sistemas Ópticos del Fraunhofer ILT.
También en este caso, la integración de la inteligencia artificial abre nuevas posibilidades: Los sistemas asistidos por IA pueden supervisar y ajustar los parámetros del proceso en tiempo real. Con ello, las desviaciones pueden detectarse y corregirse en una fase temprana, creando la base para la producción autónoma. La visión de una producción "a la primera", en la que todos los componentes se ensamblan sin errores en la primera tirada, está, por tanto, al alcance de la mano.
Producción de módulos y paquetes: eficiencia y precisión gracias a las tecnologías láser
A continuación, las células individuales se conectan para formar módulos o paquetes. La precisión desempeña un papel decisivo, sobre todo en la fabricación de módulos, ya que es necesario integrar varios cordones de soldadura sin aumentar la carga térmica de las células sensibles. Los procesos láser como la microsoldadura permiten a los usuarios adaptar sus procesos a estos requisitos de forma personalizada.
Una de las principales innovaciones del Fraunhofer ILT es el desarrollo de procesos que permiten unir con seguridad y precisión aluminio y cobre, dos materiales con propiedades físicas muy diferentes. Gracias a la guía de rayos láser de última generación, los ingenieros del instituto pueden controlar la profundidad de la soldadura para no dañar las células sensibles.
"Esta tecnología es esencial para la producción de módulos y paquetes que tienen que funcionar de forma fiable en condiciones extremas, como altas corrientes y cargas térmicas", explica Olowinsky. Un ejemplo de ello es la soldadura láser de grandes celdas cilíndricas, que el instituto de Aquisgrán ha seguido desarrollando junto con socios como EAS Batteries GmbH. En este caso, prestan atención a generar una interconexión estable y duradera entre las celdas para garantizar una larga vida útil y bajas tasas de fallo.
Además de la soldadura láser, se ha impuesto la soldadura láser, sobre todo para unir componentes sensibles al calor. Este proceso funciona a temperaturas más bajas que los métodos de soldadura tradicionales y, por tanto, protege los componentes electrónicos sensibles dentro de los módulos, lo que no sólo hace que los paquetes de baterías sean más fiables, sino también que la producción sea más eficiente desde el punto de vista energético.
Gestión de baterías e integración de sensores: inteligencia para sistemas de baterías preparados para el futuro
La gestión de baterías es uno de los retos centrales de los sistemas modernos de almacenamiento de energía. De ella dependen en gran medida la seguridad, la longevidad y el rendimiento de las baterías, así como la aceptación de la electromovilidad. Los avances en la integración de sensores y el uso de la IA ofrecen oportunidades transformadoras para cumplir estos requisitos.
Tradicionalmente, las baterías se controlan a nivel macroscópico, pero esto sólo ofrece una visión limitada de los complejos procesos que tienen lugar en el interior de las celdas. Aquí es donde la integración de la tecnología de sensores durante la producción ofrece nuevas posibilidades. Los investigadores de Fraunhofer ILT imprimen sensores directamente en los componentes, o incluso integran los dispositivos de medición inteligentes en ellos. Estos sensores hacen posible la monitorización en tiempo real, como la medición de temperaturas, fuerzas o incluso cambios químicos dentro de las baterías cuando están en uso.
"Con los sensores de fabricación aditiva, podemos controlar continuamente el estado de los módulos de las baterías y reaccionar ante posibles defectos en una fase temprana", explica Samuel Fink. Estos sensores tienen sólo unos micrómetros de grosor, son precisos y resistentes a las tensiones mecánicas y térmicas, todo lo cual los hace ideales para su uso en la batería y en los módulos de la batería. Su capacidad para proporcionar datos continuos permite un mantenimiento predictivo, que detecta posibles defectos antes de que se produzcan.
Sin embargo, la integración de la tecnología de sensores por sí sola no basta para aplicar el mantenimiento predictivo. Los sensores pueden detectar cambios en la química de las celdas, mientras que los algoritmos de IA analizan estos datos y hacen predicciones sobre la vida útil de las celdas. Los investigadores del Departamento de Ciencia de Datos y Tecnología de Medición del Fraunhofer ILT están desarrollando este tipo de algoritmos apoyados en IA que analizan grandes cantidades de datos procedentes de sensores en tiempo real. Estos sistemas también permiten adaptar dinámicamente los procesos, por ejemplo optimizando los perfiles de temperatura durante el montaje de las células o ajustando los parámetros de soldadura láser.
Reciclaje y reutilización: el camino hacia una economía circular en la tecnología de las baterías
Junto con el auge de la tecnología de las baterías, crece también la necesidad de estrategias sostenibles para recuperar materias primas valiosas. Una economía circular eficaz es esencial para reducir la dependencia de las materias primas primarias y minimizar al mismo tiempo el impacto ambiental de la producción de pilas.
En el proyecto ADIR de la UE, Fraunhofer ILT colabora con ocho socios de tres países para desarrollar un concepto de reciclaje sostenible de dispositivos electrónicos. El proyecto ACROBAT pretende desarrollar un plan de reciclaje de baterías de litio hierro fosfato antes de que penetren en el mercado a gran escala. El objetivo del proyecto es recuperar más del 90% de los materiales críticos. Junto con socios como Accurec Recycling, Fraunhofer ILT trabaja en métodos innovadores de separación y procesamiento que sean sostenibles tanto ecológica como económicamente. Los expertos en láser de Aquisgrán están desarrollando un método de caracterización en línea para evaluar con precisión la calidad del material activo.
Con su propio proceso de espectroscopia de descomposición inducida por láser (LIBS), el instituto puede identificar y separar con precisión composiciones complejas de materiales. Los investigadores quieren adaptar esta tecnología al reciclado de pilas usadas para mejorar aún más la recuperación de metales como el cobalto y el tántalo. También en este caso puede integrarse la IA para analizar las grandes cantidades de datos procedentes de las mediciones láser y optimizar el proceso en tiempo real. Esta supervisión asistida por IA permite ajustar dinámicamente los parámetros de reciclado, lo que reduce los residuos y aumenta la calidad de las materias primas recicladas.
Conclusión y perspectivas
La producción de baterías está en el centro de la transición hacia la electromovilidad y, por tanto, es el foco de innovaciones que combinan eficiencia, sostenibilidad y excelencia tecnológica. Las tecnologías y avances presentados a lo largo de la cadena de producción muestran cómo los procesos láser de última generación pueden allanar el camino hacia una industria de baterías sostenible y competitiva: desde la preparación de las materias primas y la producción de electrodos hasta el ensamblaje y reciclado de las celdas. Al mismo tiempo, los sistemas de análisis y control asistidos por IA crean una nueva dimensión del control de procesos que mejora la calidad y la sostenibilidad de la producción y reduce aún más los costes de producción.
En el futuro, los bucles de control asistidos por IA podrían permitir una producción autónoma en la que los procesos se adapten a las condiciones cambiantes en tiempo real. Además, las fuentes de rayos X accionadas por láser y las tecnologías de caracterización en línea abren nuevas posibilidades para el aseguramiento de la calidad y el análisis de materiales.
Nota: Este artículo ha sido traducido utilizando un sistema informático sin intervención humana. LUMITOS ofrece estas traducciones automáticas para presentar una gama más amplia de noticias de actualidad. Como este artículo ha sido traducido con traducción automática, es posible que contenga errores de vocabulario, sintaxis o gramática. El artículo original en Inglés se puede encontrar aquí.