Recubrimientos resistentes al desgaste eficientes en recursos y rentables gracias a un nuevo proceso de recubrimiento híbrido
Aumento de la dureza de hasta un 30%.
Un equipo de investigadores del Instituto Fraunhofer de Tecnología de la Producción (IPT) de Aquisgrán ha desarrollado un proceso híbrido de fabricación aditiva que combina el revestimiento por láser de alambre y de polvo (LMD). El nuevo proceso puede utilizarse para aplicar revestimientos protectores de acero para herramientas de alta resistencia a las piezas de trabajo y reparar los defectos superficiales a bajo coste. Los recubrimientos para herramientas producidos de esta manera son más resistentes al desgaste, y consumen menos recursos y son más económicos que los producidos por otros métodos. Tras el éxito de las series de pruebas con componentes de herramientas, está previsto utilizar el proceso para mecanizar componentes hidráulicos.
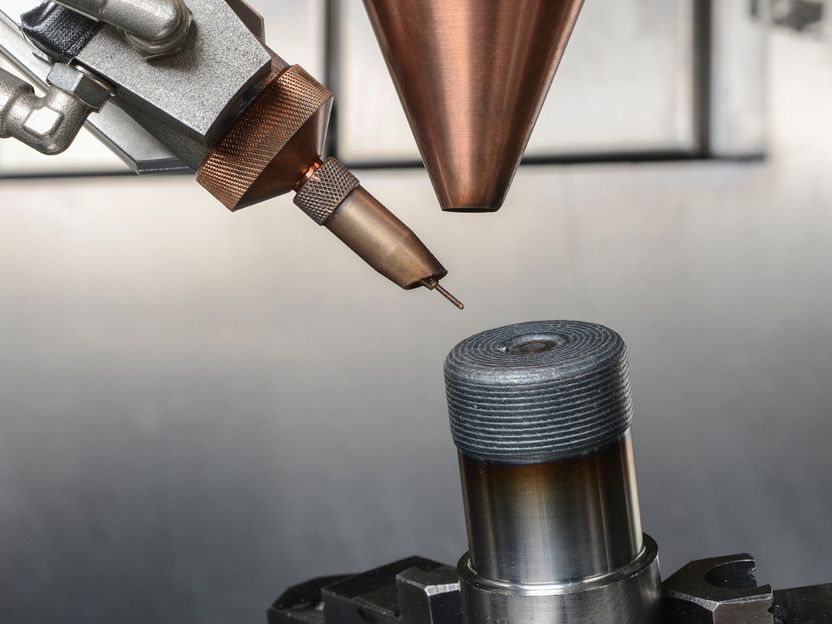
La combinación de alambre y polvo probada en el Fraunhofer IPT permitió aumentar la dureza del material hasta un 30%.
Fraunhofer IPT
Los procesos de fabricación aditiva, como el revestimiento por láser (LMD), se utilizan para fabricar componentes u optimizarlos localmente. En el LMD, se enfoca un rayo láser sobre la superficie del componente; al mismo tiempo, se alimenta y funde un material de relleno, normalmente en forma de polvo o alambre. El LMD es muy adecuado para aplicar revestimientos protectores a componentes sometidos a grandes esfuerzos, reparar zonas dañadas y cambiar la geometría de las piezas, incluso durante períodos cortos.
La combinación de alambre y polvo es flexible y rentable
Un equipo de científicos del Fraunhofer IPT, junto con sus socios internacionales del proyecto, ha desarrollado una variante híbrida de la soldadura por acumulación láser en el proyecto de investigación "MatLaMeD", recientemente finalizado, en la que se procesan simultáneamente alambre y polvo. Al añadir partículas de material duro en forma de polvo al material del alambre, el equipo consiguió por primera vez ajustar selectivamente importantes propiedades del material, como la dureza y la tenacidad de las capas aplicadas. Además, el proceso es mucho más rentable que un proceso de polvo puro y ofrece mayor flexibilidad de material que un proceso de alambre puro.
Combinaciones individuales de materiales para diferentes requisitos
Para identificar las mejores combinaciones de materiales para diferentes aplicaciones, los científicos probaron numerosos materiales. Como materiales de alambre para la serie de pruebas prácticas, seleccionaron finalmente un acero para herramientas en caliente con buena estabilidad estructural y un acero de baja aleación que puede soldarse bien. Como materiales en polvo, utilizaron el cromo (Cr) como elemento formador de carburo y refinador de grano y el carburo de titanio (TiC) como fase dura en la serie de pruebas.
Aumentos de la dureza de hasta el 30%.
Al combinar el alambre y el polvo, los investigadores pudieron ajustar con flexibilidad la composición del material para cada aplicación. La adición del material en polvo permitió cambiar selectivamente la microestructura de los aceros para herramientas y aumentar la dureza de los recubrimientos aplicados: incluso la adición de pequeñas cantidades de carburo de titanio permitió aumentar la dureza hasta un 30%. "Con el nuevo proceso, ahora podemos responder de forma rápida y flexible a diferentes cargas térmicas, químicas y mecánicas, ya que podemos ajustar la tenacidad y la dureza con una precisión milimétrica", afirma el director del proyecto, Marius Gipperich. Según el científico de Aquisgrán, el nuevo proceso es una herramienta perfecta para minimizar el desgaste de la superficie y prolongar considerablemente la vida útil de los componentes.
Serie de pruebas prevista para el mecanizado de componentes hidráulicos
Los resultados positivos del proyecto "MatLaMeD" proporcionan a los investigadores una base para seguir desarrollando el nuevo método para desarrollar otros sistemas de materiales con propiedades especiales. También tienen previsto utilizar el proceso LMD híbrido en diversos ámbitos de aplicación, como el mecanizado de herramientas de conformación o el tratamiento de las capas de desgaste por fricción de los componentes hidráulicos.
Los investigadores están probando actualmente las posibilidades de utilizar el proceso LMD híbrido en la producción de sistemas de revestimiento graduado. Para ello, quieren aumentar al máximo el contenido de carburo de titanio en la mezcla de materiales. Dado que el carburo de titanio puede provocar elevadas tensiones residuales que pueden aumentar la susceptibilidad a las fisuras durante la soldadura, el equipo de investigación de Aquisgrán quiere ajustar el contenido de TiC capa por capa.
El proyecto "MatLaMeD - Desarrollo de nuevos procesos para el revestimiento láser híbrido" fue financiado en el marco de la iniciativa de financiación "Innovaciones para la producción, los servicios y el trabajo del mañana" del Ministerio Federal de Educación e Investigación de Alemania (BMBF).
Nota: Este artículo ha sido traducido utilizando un sistema informático sin intervención humana. LUMITOS ofrece estas traducciones automáticas para presentar una gama más amplia de noticias de actualidad. Como este artículo ha sido traducido con traducción automática, es posible que contenga errores de vocabulario, sintaxis o gramática. El artículo original en Inglés se puede encontrar aquí.